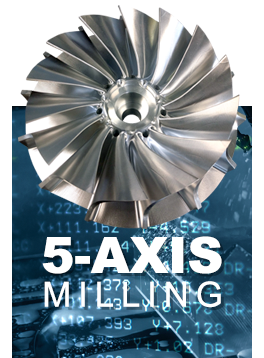
SUMMARY
If you need advanced 5-axis machining services, you have come to the right place.
Solid Machine performs high-speed, simultaneous 5-axis milling on up to 3,000 parts per month by both flank and point milling including turbocharger impellers, aero-engine spacers, compressor impellers, turbines, pumps, blades/vanes, and custom hardware up to Ø26.0” (660mm).
Our talented team has decades of experience in the machining of rotating bladed turbomachinery hardware in a wide range of materials to the tightest dimensions and most stringent specifications. We are more than a “chip cutter” and can suggest more efficient manufacturing methods, processes, and design changes that will meet your needs, while lowering your production costs.
Whether you need a complex prototype or high-volume production, contact us to experience the difference Solid Machine can make in bringing your product or vision to life.
SHOWCASE
We hope the following gallery provides a glimpse at the diversity, quality and workmanship of our manufacturing solutions.
SOLUTIONS & SPECIFICATIONS
Max Diameter: |
26.0” (660mm) |
Max Height/Length: |
24.6” (625mm) |
Max Weight: |
4,400 lbs (2000 kg) |
Materials: |
|
Tolerances: |
+/- 0.0001” to 0.0002” depending on the feature, alloy, etc. |
Internal Capabilities: |
|
Subcontracted Services: |
|
Lead Time: |
Quoted on a job by job basis, but typically under 6 to 8 weeks ARO. |
Software: |
|
File Formats: |
We have yet to receive a model or drawing file we could not open. Try us…we’ve got you covered. |
Solid Machine | 61 Airport Dr.- Unit 1 | Rochester, New Hampshire 03867
Phone: (603) 332-5511 | E-mail: info@solidmachinenh.com